BAPRO Chassis Dyno 4WD
The secret is repeatability.
A specific dynamometer for your needs.
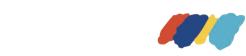
4WD BPA-4R HP Linked
Mechanical synchronization between shafts.
-
Valid for electric vehicles.
-
Maximum speed 360km/h
-
Maximum measurable power 2000HP
-
Roller diameter: 400 mm
-
Roller width: 700 mm
-
Maximum axle weight: 2,500 kg
-
Direct mechanical linkage between front and rear axles, which can be fully deactivated by software
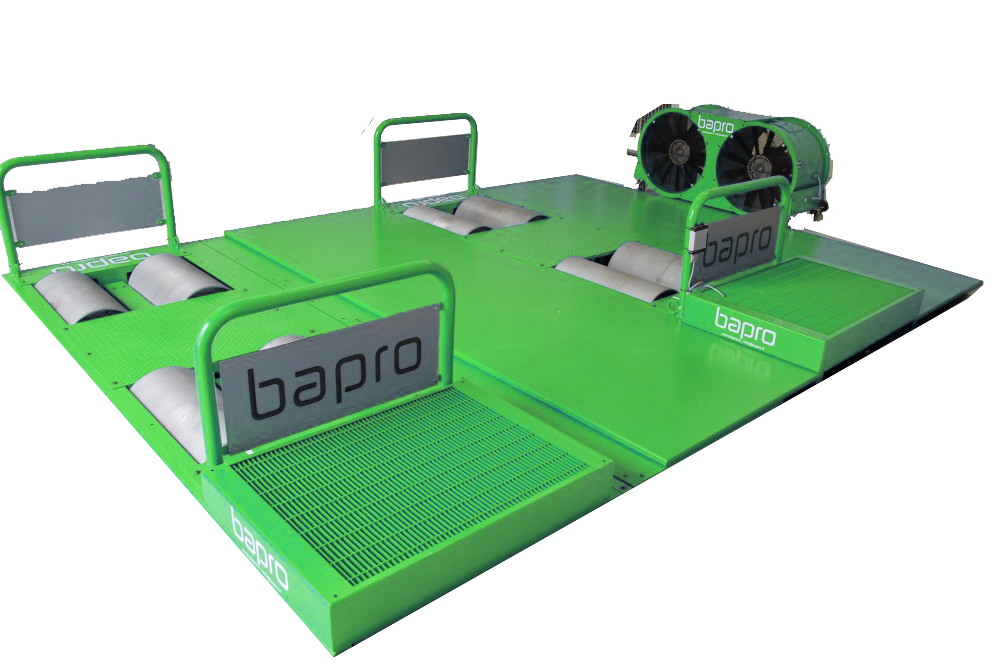
4WD BPA-4R HP
Electronic synchronization between axles.
-
Valid for electric vehicles.
-
Maximum speed 360km/h
-
Maximum measurable power 2000HP
-
Roller diameter: 400 mm
-
Roller width: 700 mm
-
Maximum axle weight: 2,500 kg
-
Electronic linking by software
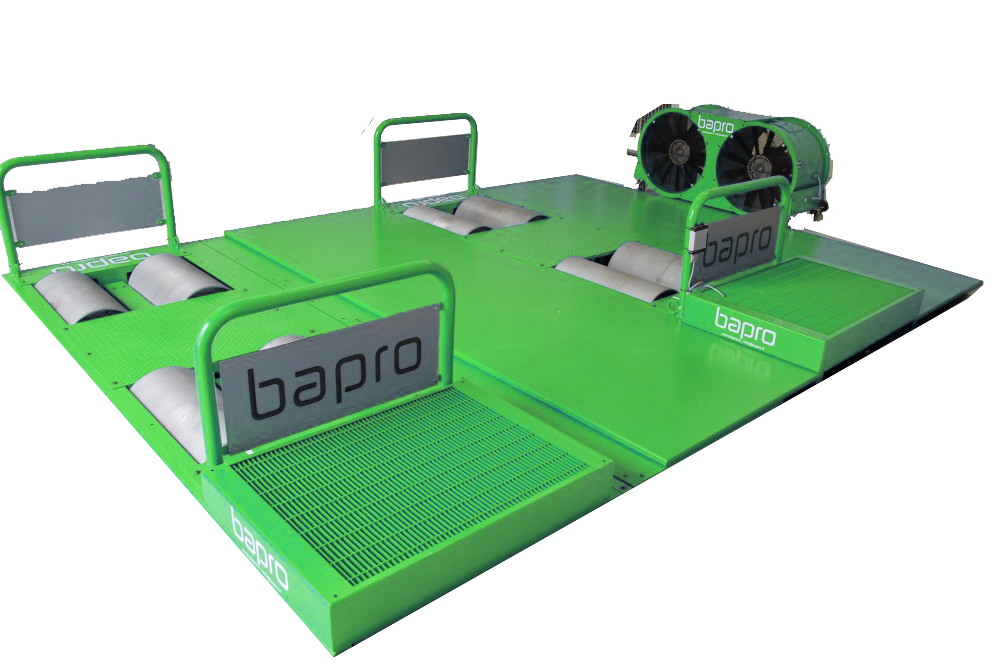
4WD BPA-4R S
Electronic synchronization between axles.
-
Valid for electric vehicles.
-
Maximum speed 250km/h
-
Maximum power 800HP / 400HPxAxis
-
Roller diameter: 240 mm
-
Roller width: 660 mm
-
Maximum axle weight: 2,500 kg
-
Electronic linking by software
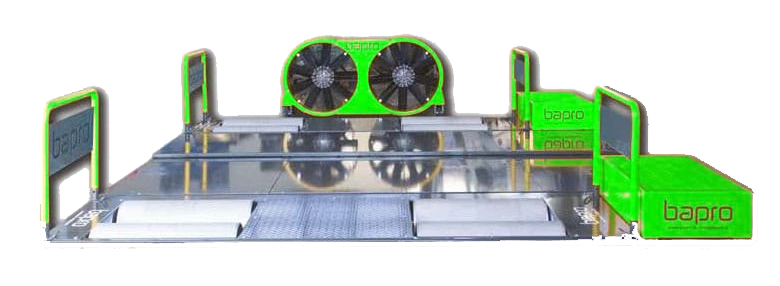
Don't know which dynamometer you need?
Contact us and an agent will answer your questions and help you choose the best option for your business.
Frequently Asked Questions
No! Inertial dynamometers are old-fashioned measuring instruments that have lost their usefulness and have become obsolete.
They do not measure torque and power, but perform a mathematical calculation and provide an imprecise value that varies from one test to another. Bapro does not manufacture inertial dynos but brake dynos, designed down to the smallest detail to take advantage of all the benefits offered by this type of technology.
In brake dynamometers, the power is measured by the load cell in order to obtain a highly accurate and repeatable data. The power is measured with a controlled acceleration that reproduces the actual behavior of the vehicle on the road and is adapted to its performance. In this way, the engine’s operation is identical to its behavior on the road and the crankshaft power data provided by the bench is accurate and reliable. In addition, the presence of the eddy current brake and a highly advanced electronic control system allows many other tests useful for diagnostics, tuning and motorsport, such as road simulations, constant rpm tests and mapping, to give just a few examples.
No! A brake-transformed dyno is, to all intents and purposes, an inertial dyno to which a brake and an electronic control system are added. This type of dyno is based on the concept of inertial dyno, which, by their nature, have a series of limits that prevent them from being effectively transformed into braking dyno.
This is true for all dynos that are available on the market with both versions (inertial and braking). Bapro’s dynos, on the other hand, are exclusively of the braking type by means of eddy current braking. Among the limits of the inertial benches that are transformed into braking type benches is, for example, the great weight of the rollers, which in the inertial benches is mandatory precisely to create the inertial mass to be accelerated. On the other hand, in braking power benches, the weight of the rollers must be reduced to a minimum in order to achieve maximum precision and repeatability. For that reason, Bapro’s rollers are hollow and have been lightened: the inertial mass is minimal and the measured power responds perfectly to the value generated by the motor. Another significant limit is the grip of the rollers, since on inertial benches acceleration is very fast during power tests, and not much grip is required (that is why the rollers are often smooth or, at most, knurled by upsetting). However, if they are transformed into braking-type benches, this grip is necessary, otherwise the tires will slip on the rollers and significantly falsify the test, as well as creating the risk of tire explosion. The problem is that during the transformation it is not possible to replace the rollers. That is why the rollers of Bapro’s benches – originally designed as brake benches – are knurled by cutting (with chip removal), to provide high grip and an undamaged surface even after thousands of tests, allowing reliable data and repeatable results to be obtained.
Bapro’s dynos, on the other hand, are exclusively of the braking type by means of eddy current braking. Among the limits of inertial benches that are transformed into braking type benches is, for example, the large weight of the rollers, which in inertial benches is mandatory precisely to create the inertial mass to be accelerated. On the other hand, in braking power benches, the weight of the rollers must be reduced to a minimum in order to achieve maximum precision and repeatability. For that reason, Bapro’s rollers are hollow and have been lightened: the inertial mass is minimal and the measured power responds perfectly to the value generated by the motor. Another significant limit is the grip of the rollers, since on inertial benches acceleration is very fast during power tests, and not much grip is required (that is why the rollers are often smooth or, at most, knurled by upsetting). However, if they are transformed into braking-type benches, this grip is necessary, otherwise the tires will slip on the rollers and significantly falsify the test, as well as creating the risk of tire explosion. The problem is that during the transformation it is not possible to replace the rollers. That is why the rollers of Bapro’s benches – originally designed as brake benches – are knurled by cutting (with chip removal), to offer high grip and an undamaged surface even after thousands of tests, thus providing reliable data and repeatable results.
No roller bench is capable of actually measuring the power to the wheel, as it is physically impossible with this type of instrument.
The dyno that is not able to measure the power to the crankshaft and that provides the power to the wheel, in reality what they are indicating is a very inaccurate data, obtained by means of estimated performances that do not take into account the variability of the test conditions. It is enough to think that in order to significantly alter the power at the wheel, it is sufficient that there is a difference in the tightening of the vehicle’s anchoring belts, in the tire pressure or even in the temperature between one test and another.
The only power that can be used as a reference to get accurate data with which to make comparisons is power to the crankshaft.
Bapro’s prestigious customers have awarded it important recognitions for the total accuracy in the measurement of crankshaft power, thanks to the comparison with other engine test benches.
The declared maximum power is indicated in the technical information of each product. It should be specified that these are power values that the bench can actually brake in stationary tests, such as the constant speed test or mapping. The performance during dynamic tests for measuring power and torque curves is actually higher, as also demonstrated by the tests carried out by our customers and published on the website. The first limit of a dyno is not the brake performance, but the grip provided by the rollers. Indeed, before reaching the braking torque limit, the problem of slippage arises, something that does not occur on Bapro’s dyno thanks to the characteristics of our rollers. When a dyno declares power values of thousands of horsepower per axle, it is actually declaring dynamic powers (in acceleration phase), which is tantamount to indirectly admitting that they measure power mainly in an inertial mode rather than braking, with all the limits that this entails (described in the previous points 1 and 2).
Bapro’s dyno has been designed with a modular concept, so it is possible to buy a two-wheel drive dyno (4×2 BPA-2R) and change later to a four-wheel drive dyno (4×4 BPA-4R), simply by adding a second dyno and the offset system that allows adjusting the length according to the wheelbase of the vehicle.
This allows you to start with a smaller investment and then, without “wasting” anything, you can buy the necessary components to complete the 4×4 dyno with which to test all types of cars. The modular concept also extends to the type of installation, i.e. the dyno can be mounted on the ground or embedded in a pit, as preferred, without the need for additional accessories.
If we transfer our concept of the car dyno to the motorcycle sector, we see that the largest possible contact surface is required for measuring and braking certain powers. From this point of view, the surface area offered by a single roller is insufficient, especially when working with very powerful or very high torque motorcycles (e.g. Harley, Ducati and twin-cylinder motorcycles in general).
Bapro’s dynamometer dyno is available in both single-roller version (BPM-1R) and double-roller version (BPM-2R). Also in this case, the modularity of the project allows to buy the first version (very suitable for those who work mainly with scooters or medium-low power motorcycles) and then add the second roller when expanding the clientele to include higher performance or competition motorcycles.
Thanks to the lightened rollers, the double-roller version offers all the advantages of an extremely high grip (impossible to achieve on any other dyno!), which not only eliminates maximum power limits but also makes it possible to test lower powers with maximum precision (as in the case of small electric scooters).
The software is very simple and intuitive, so no training course is required; however, the installation of the instrument includes a complete course given by our technicians. The software version provided in the standard configuration of the dyno is complete and allows to perform all possible tests with the dyno, in simple and quick steps.
All the bench functions can be used by means of the remote control included, so that only one operator is needed. Thanks to the manual supplied with the bench and the assistance of our technicians and engineers, it is possible to learn how to use the instrument very quickly and to get the most out of it even without a training course.
BAPRO provides with all dynamometers a fully functional version of the chassis dynamometer software, without ADD-ONS or additional costs!
The electronic control system of the bench is built into the instrument, so no special computer is required and no hardware cards need to be installed in the PC.
Bapro’s software is installed in a few minutes on a commercial PC.
It is sometimes said that single-roller dynamometer dyno’s are able to simulate roads better than double-rollers. Unfortunately, to achieve this, an 800-millimeter-diameter roller is required; otherwise, there is not a large enough flat surface on top to provide the traction needed to capture the full power of the car.
That’s the reason why all single-roller dynamometer dyno’s have large rollers, but never enough!
To be more precise, the contact area between the tire and the roller is less than that which occurs on the road, and is approximately one third of the area available on double-roller dynamometer dynamometers.
This is due to the presence of a single contact area at the top of the roller (as it is easy to guess, not being flat like the road, the contact surface is reduced).
Less surface area = less traction = less maximum power measurable on the dyno.
In conclusion, the car is much more likely to cause the tires to skid rather than transmit all of its energy to the rollers for accurate measurement.
Dual-roller dynamometer dynamometers solve this problem by simply doubling the number of rollers in contact with the tires.
In addition, a large roller produces a large inertia and this is detrimental to accuracy (larger rollers = greater inertia at equal roller weight = inaccurate and non-repeatable measurements; see the first “FAQ”, regarding inertial dyno).
Double-roller dynamometer dynamometers do not present this problem because their rollers have low inertia.
Another aspect is that all single-roller dynamometer dyno’s require the realization of a deep pit, since the rollers are very large and consequently the frame is very high (e.g. 800 mm deep). Bapro’s double-roller dynamometer dyno only requires a 450 mm deep pit.
Finally, if you search for “dyno accidents” on YouTube, you will find many videos of accidents involving cars on single-roller dynamometer dyno’s. In this situation, the car is in an unstable position on top of the roller and if the belts break or even just come loose, the car can come off the dyno. In this situation, the car is in an unstable position on top of the roller and, if the straps break or even just come loose, the car can come off the dyno.
The likelihood of something like this happening on a double-roller dyno is much lower, since the car is in a stable position between the two rollers and has no way of falling or sliding off the bench.